- Top
- Products & Technologies
- Smart Factories
- Torque & Quality Control Systems
Torque & Quality
Control Systems
Torque & Quality
Control Systems
Improve measurement and inspection with an optical cutting method inspection system.
Torque Control Systems
Digital transformation DX / Digital twin
- It is essential to take measures to prevent forgetting to fasten bolts and incorrectly setting torque values.
- We promote automating acquisition of various inspection data while utilizing IoT technology. We also work to improve quality and operational efficiency by ensuring traceability.
Operation navigation
- IoT technology is combined with actual work instructions to implement a system that prevents work errors. The system simultaneously improves on-site efficiency and helps pass on skills.
Quality Control Systems
Prepreg lamination accuracy measurement technology PAT.
- Features
-
- Capable of measuring groove dimensions
- Optical cutting method measurement enables measurement of grooves and gaps.
- Supports a wide variety of surface inspections
- Detects adherence of foreign matter.
- High-speed measurement and multiple measurement point settings
- It is capable of making 30 measurements per second at a travel speed of 1 m/min.
- Real-time tracking measurement
- Real-time control prevents data measurement omissions at measurement points. Inspection time is fast due to automatic measurement.
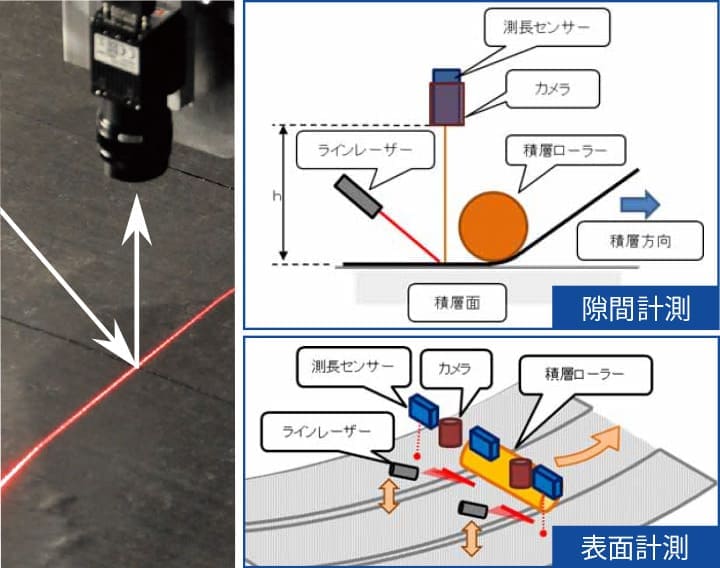
Roundness measuring device PAT.
- Features
-
- Optical cutting measurement with ring laser
- Capable of outputting roundness, coaxiality, bore and diameter dimensions without contact.
- No need for positioning
- Simply place the workpiece on the jig, and it will optically correct the amount of zero-point misalignment.
- Tilt correction function
- The standard tilt correction function reduces the time required to set the workpiece on the jig.
- High-speed measurement
- Measurement time is 3 seconds per location, enabling high-speed cylinder inspection.
- 100% inspection in-line
- Laser light scanning allows for 100% in-line inspection.
- High-precision
- Measurement accuracy is 5/100mm. The 3D cylinder display and the cut-off circle display enable the user to determine normality or abnormality at a glance.
- Low cost
- You can cut operating costs compared to contact measurement using a probe.
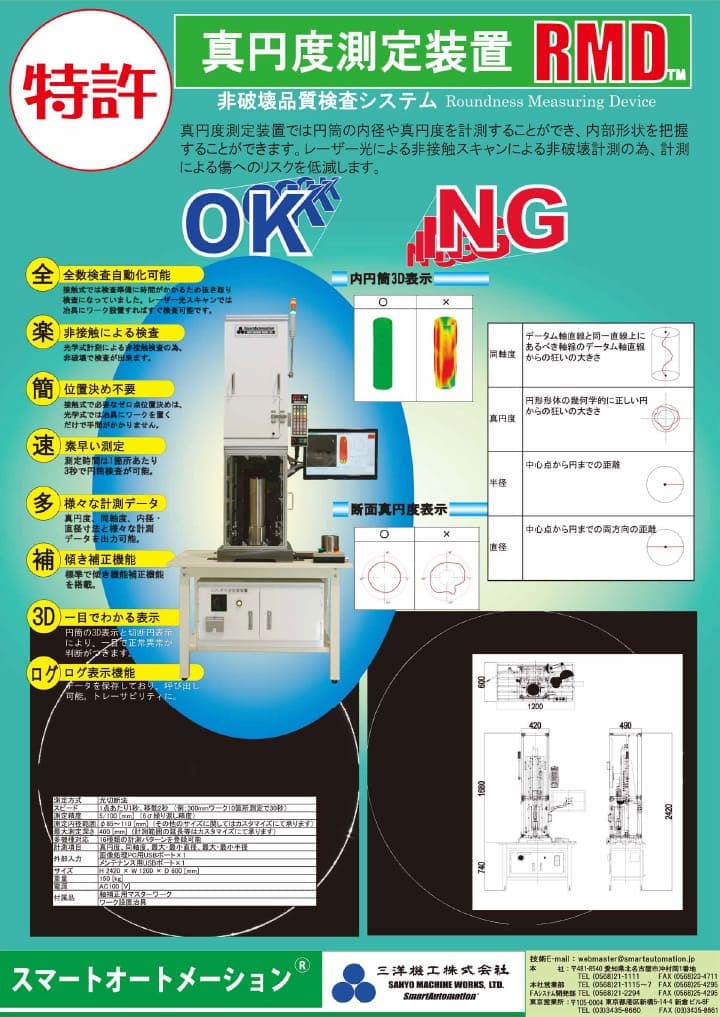
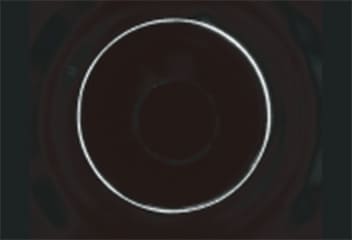
measurement
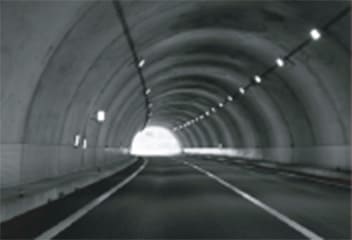
detection
Examples of Adoption
Torque Control System for Train Manufacturing utilizing Smart Digital Torque Wrench
West Japan Railway Company Hakata Rolling Stock Depot
- Problem faced before adoption
-
- 1. The decline in the number of producers threatened to affect the production process due to the resulting labor shortage at the Hakata Rolling Stock Depot.
- 2. Mistakes in setting torque values and forgetting to fasten bolts were occurring in bolt fastening operations.
- Technology Adopted
-
- Operation navigation system
- Wireless Smart Digital Torque Wrench
- Reasons for Technology Selection
- Our hybrid torque wrench is equipped with a double-fastening prevention function. This function enables error-prevention. Torque values are automatically set according to the work to be performed, which also prevents torque value setting errors. In addition, information on actual fastening torque values can be collected from torque wrenches to create a work history traceability system.
- Outcome and Effectiveness
- Our standard operation navigation, makes it easy to establish a system to prevent operating errors by combining the latest IT technology based on Industry 4.0, and actual work processes. This has improved the work efficiency of the manufacturing site.
Bolt Fastening Operations Torque Control System utilizing Smart Digital Torque Wrench.
TAKENAKA CORPORATION
- Problem faced before adoption
-
- 1. Inspection accuracy in plumbing construction was dependent on the skill level of the operator.
- 2. Mistakes in setting torque values and forgetting to fasten bolts were occurring.
- Technology Adopted
-
- Operation navigation system
- Wireless Smart Digital Torque Wrench
- Reasons for Technology Selection
- Adopting Sanyo’s Operation Navigation System and Smart Digital Torque Wrenches reduces variability due to operator skill level. DPW Series Smart Digital Torque Wrenches can automatically set the fastening torque value, preventing torque value setting errors and increasing reliability. Meanwhile, a Piping Torque Control System combined with 3D-CAD, streamlines the construction process and enables the collection of torque management data. This can reduce variations in accuracy due to operator skill and improve quality.
- Outcome and Effectiveness
- The introduction of the Smart Digital Torque Wrench has effectively prevented torque value setting errors and forgetting to fasten bolts, thereby improving the overall quality of the customer's operations. Also, having the torque wrench transmit the actual torque values establishes a work history traceability system, and improves quality assurance and quality management. Our operation navigation system supports “industrial transformation”, and makes it easy to establish a system to prevent operating errors by combining the latest IT technology, and actual work processes. This has improved the work efficiency of the manufacturing site.
Product Catalog
※Japanese Only